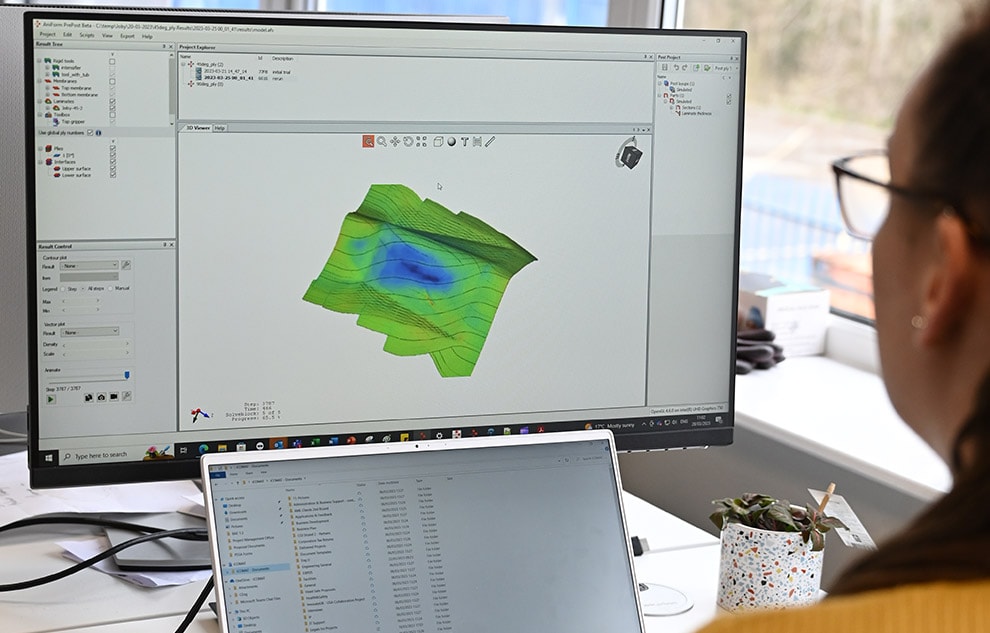
Industry-leading design
Optimisation of components and structures with an end-to-end workflow
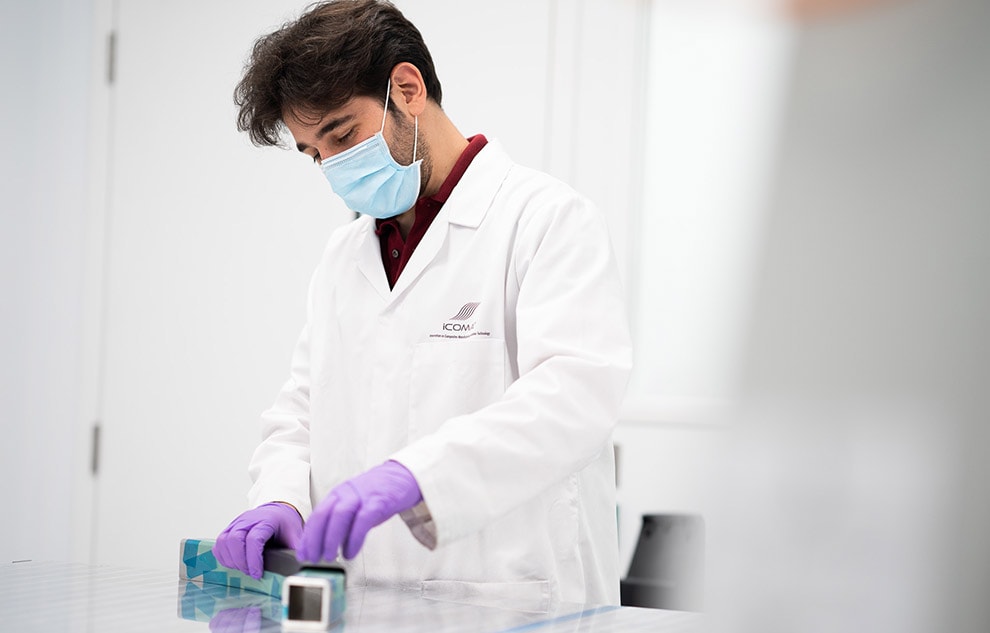
Advanced prototyping
Material characterisation and testing, virtual and physical prototyping
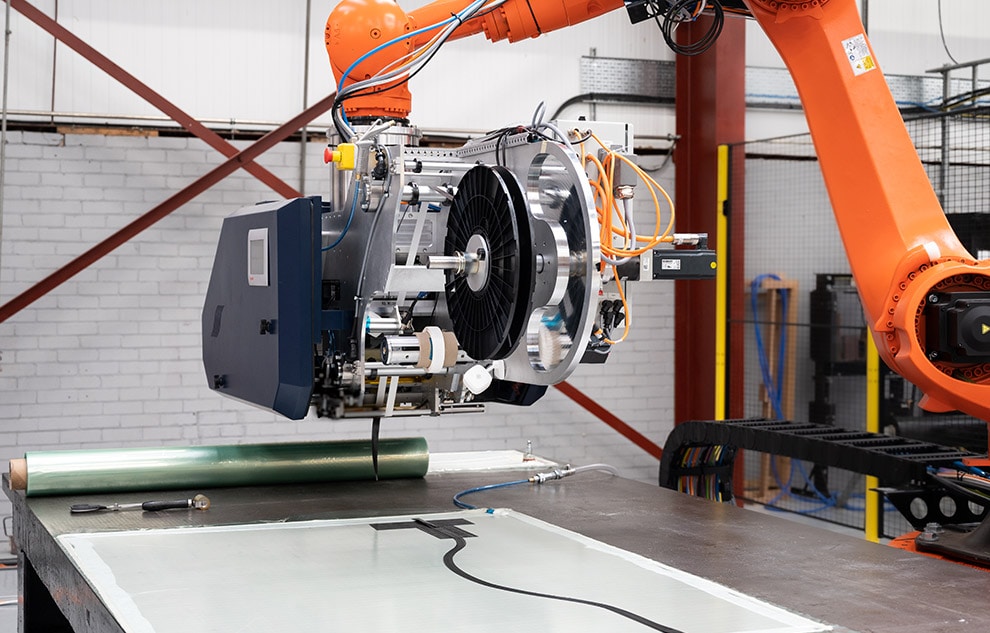
State-of-the-art production
Fully automated flexible manufacture ensuring rate, quality and repeatability
At the core…
The innovative RTS production cells
The patented RTS technology paired with state-of-the-art robotic equipment.
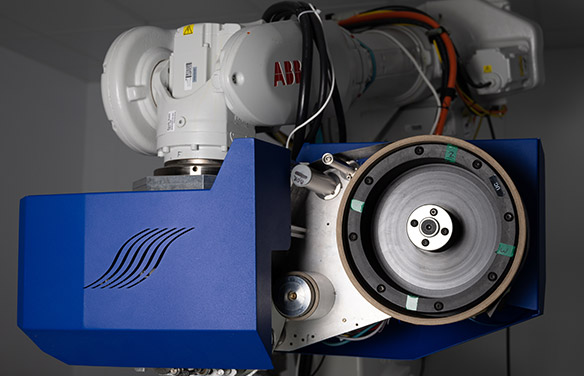
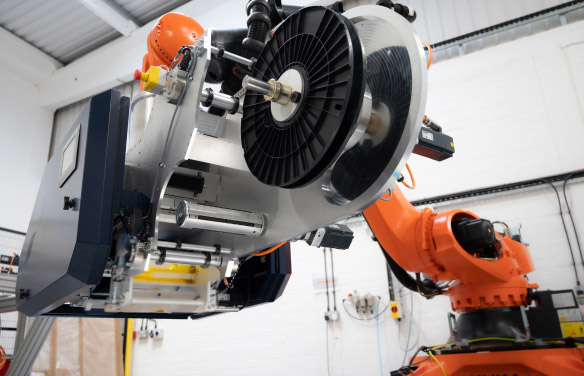
Specifications
Material types | Thermoset, dry fibre and comingled thermoplastic as UD, woven or NCF |
Heat Source | Multi-lamp Infrared |
Tape cutter | 4-axis Ultrasonic |
Control system | Siemens 840d & Beckhoff |
Minimum steering radius [mm] | 50 |
Maximum shear angle2 [degrees] | 45 (fabric) – 70 (UD) |
Minimum course length2 [mm] | 100 |
Gap tolerance [mm] | +0/-2 |
Material width [mm] | 12.5 – 200 |
Material thickness [mm] | 0.1 – 1.0 |
Maximum mould curvature [mm] | Dependent on head/ material configuration |
Deposition speed [m/s] | Straight: 1.0 Steering: 0.3 Cutting: 0.1 |
Deposition rate [kg/h]* | 10 – 100 |
Material roll diameter | Up to 500lm on 12’’ core |
Material roll compatibility | All standard core sizes from 3” – 12”, also compatible with Hafner cores |
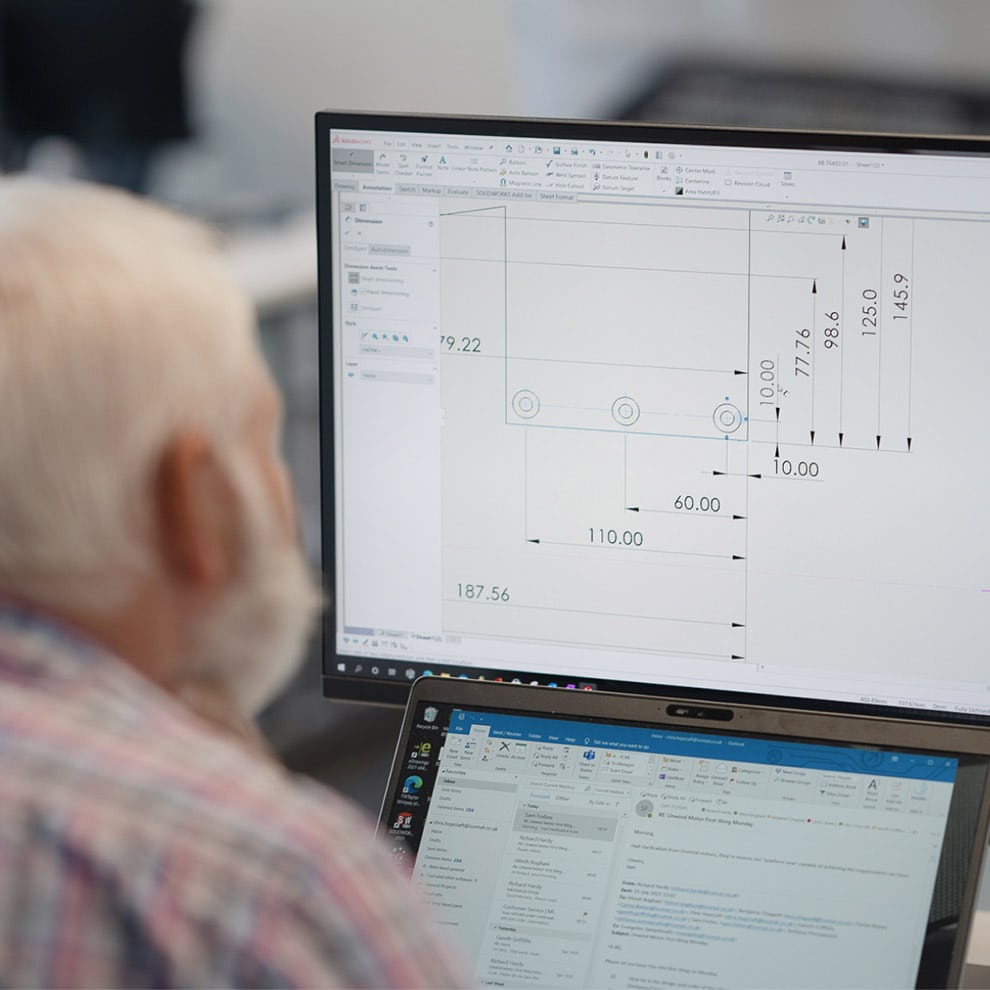
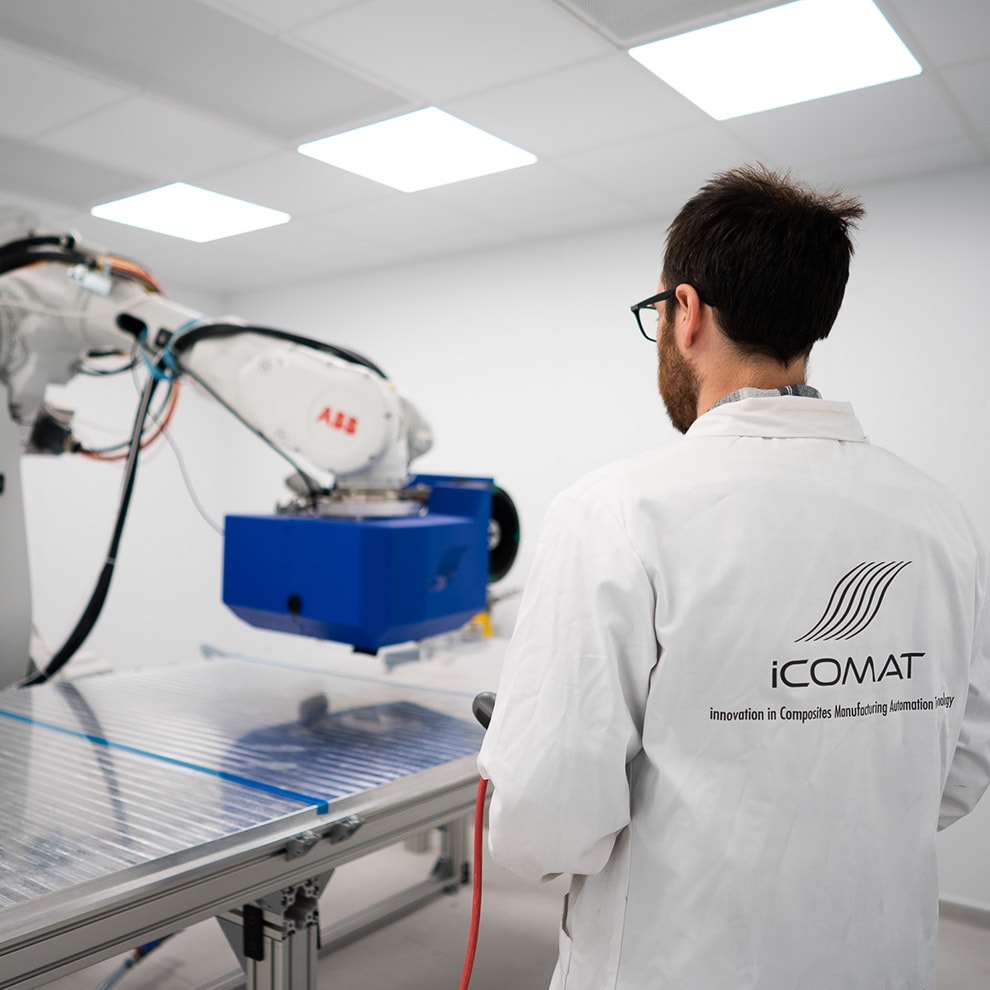
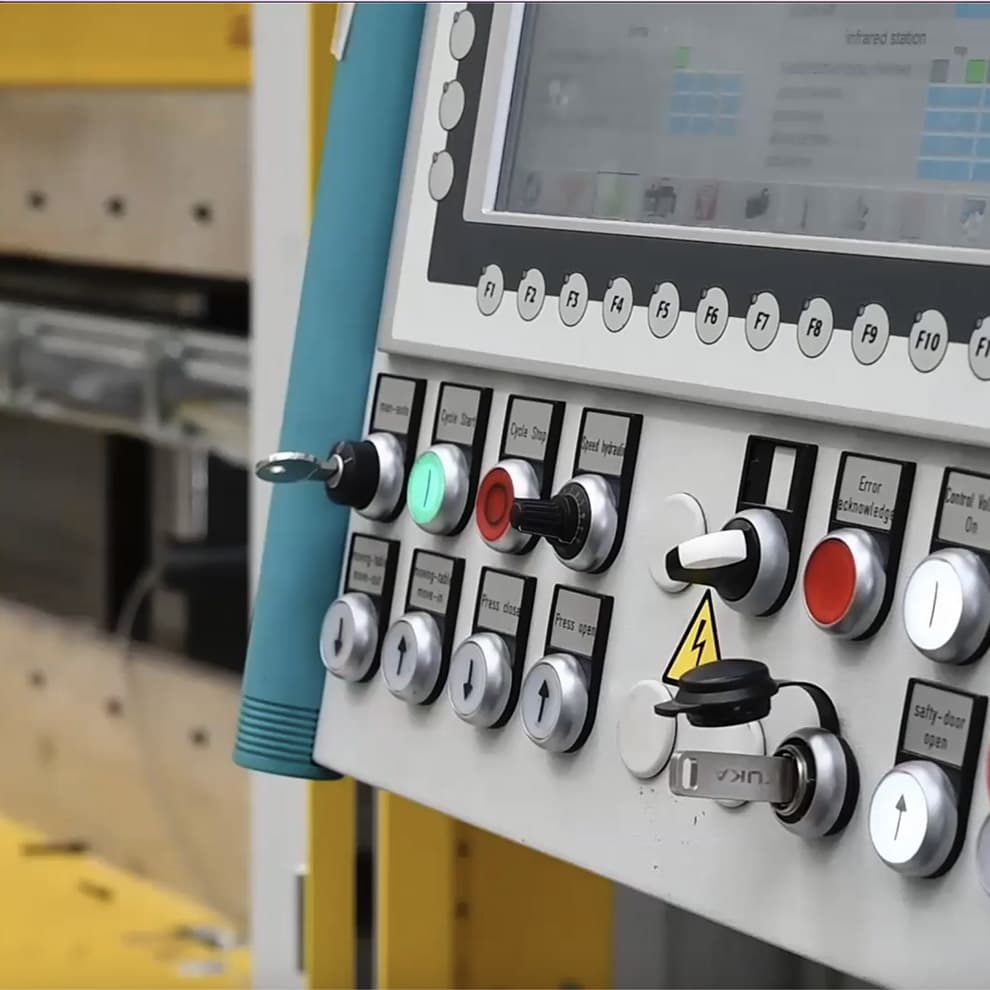
Production Site – Gloucester, UK
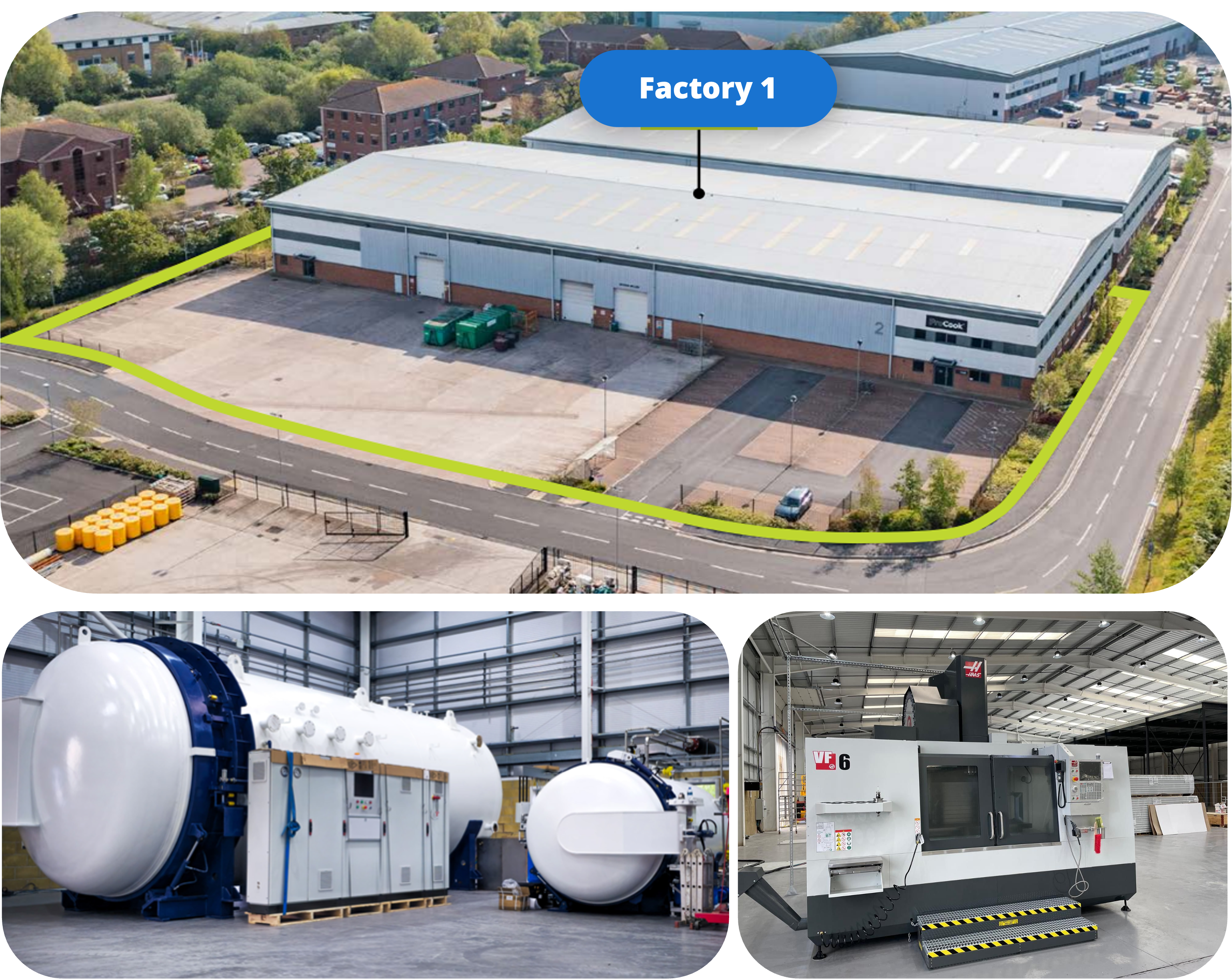
State-of-the-Art Automated Manufacturing facility with
6 RTS machines (2 x prepreg, 2 x dry fibre, 2 x 3D RTS)
- Over 40,000 sq ft Production Facility
- ISO Class 7 Clean Room – 5,000 sq ft
- 6 x RTS Lay-up – 10 m x 4 m
- Multiple Laser Projection Systems
- Automated Ply Cutters
- 2x Autoclaves – largest 6 m x 3 m
- 2x CNC Machines – largest 6 m x 3 m x 1.5 m
- Composite Painting Capability
- Press Moulding Capability
- Hot Drape Forming
- Comprehensive Inspection
- Press Moulding Capability
- Hot Drape Forming
- Large Freezer storage (data recording)
- Full FEA capability (multiple seats)
- Full Planning and MRP in “Real Time”
- Laser Projection for Lay-up & Assembly
- Full Spray / Bake Paint Facility
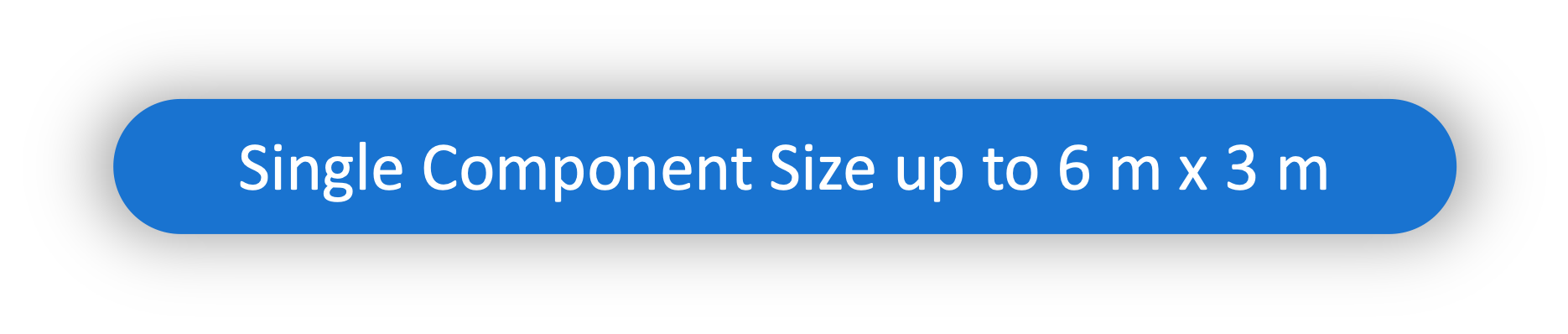